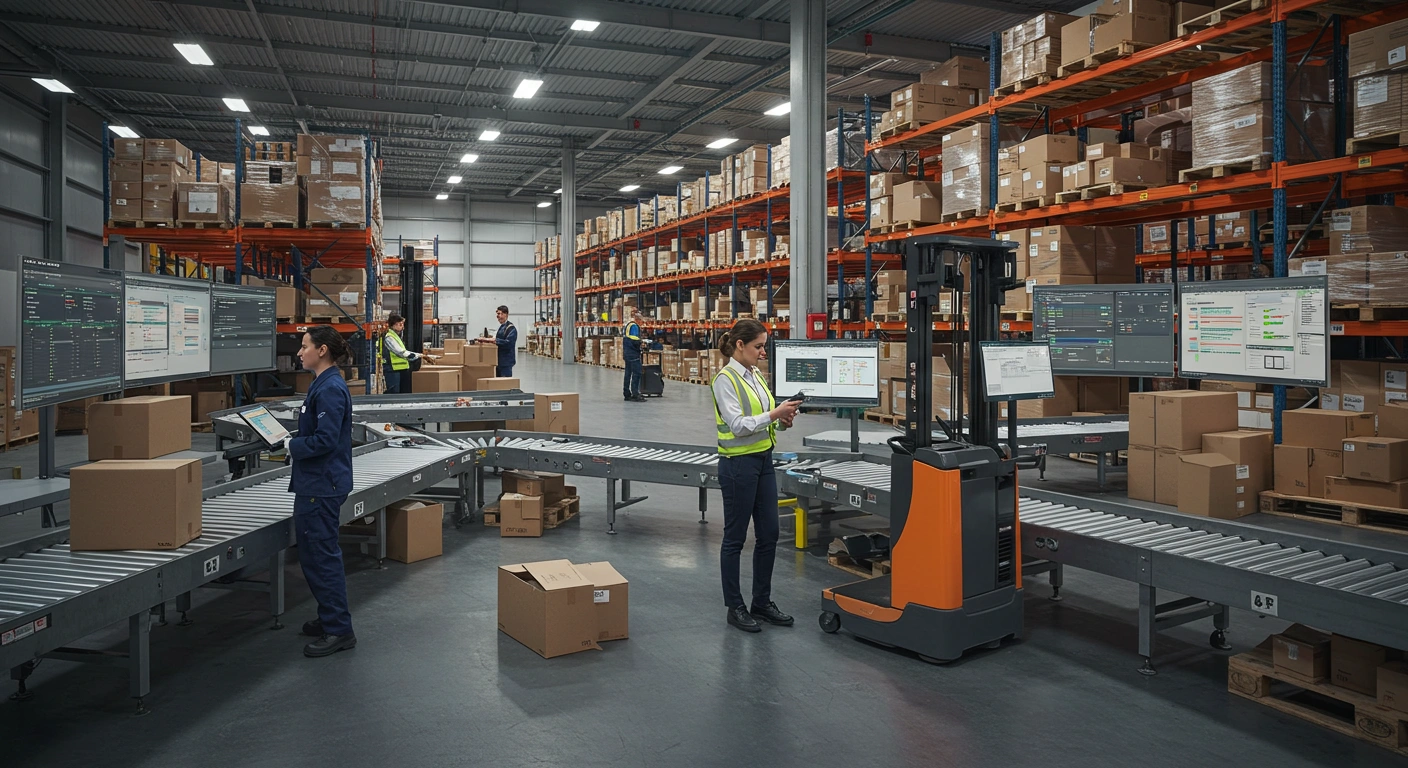
For modern businesses, warehouse management is one of the most fundamental building blocks of the supply chain. This process is more than just a place where products are physically stored, it is a strategic function that ensures inventory is managed at the right time, in the right place and at the most cost-effective rate.
An effective warehouse management system directly increases operational efficiency and reduces costs. A well-organized warehouse ensures faster and more error-free preparation of orders, maximizing customer satisfaction.
In this article, we will take a deep look at the basic processes that are vital for successful warehouse management, the modern technologies used, and the tangible benefits they will provide to your business. Read on to discover the steps to transform your warehousing operations from a cost item to a competitive advantage.
What is Warehouse Management?
Warehouse management is the planning, organization and control of all operations in the warehouse that houses a company's inventory. This process includes all the steps from receiving goods to storing them, picking them up to order and shipping them.
To better understand this process, you can imagine a large, modern library. Just as each book is in a specific category, on a shelf, and in a row, each product in the warehouse has a defined location and code in the system.
Just as a librarian can find the right book for a reader in seconds, effective stock management ensures that the right items for a customer order are found and prepared quickly and accurately. Without this system, the stock would become a chaotic pile of books where it would be nearly impossible to find what you were looking for.
Warehouse management therefore aims to maximize space utilization and minimize operational costs while maintaining the security and integrity of inventory. The main goal is to make the journey of products within the warehouse smooth and efficient.
Warehouse Management Basics
A successful warehouse management process consists of several key elements that work in harmony with each other. Each of these components plays a critical role in ensuring the smooth operation of the supply chain and operational efficiency.
- The first step of the process is to receive the incoming products in the correct quantity and without damage and record them in the system.
- The goods received are placed in designated storage areas with the aim of the most efficient collection.
- It is the physical storage process that involves the most efficient use of warehouse space while ensuring the safety of products.
- It is the accurate and rapid collection of products in customer orders from their locations in the warehouse.
- The collected products are packaged, labeled and loaded onto the shipping vehicle to be sent to the customer.
- It includes periodic counts and record management processes to ensure accuracy of stock levels and prevent losses.
The integrated and error-free management of each of these basic elements forms the basis of an efficient warehouse management system. Utilizing technology is one of the most important factors that facilitate the harmonious operation of these complex processes.
Getting Started with Warehouse Management
When you decide to set up an effective warehouse management system for a business, the first step to take is to analyze your current situation in detail. This analysis should cover everything from the physical structure of your warehouse to the technology used, from human resources to current processes. It is not possible to determine the right solutions without a full understanding of your situation.
The type, size and characteristics of your current inventory should be determined. The answers to questions such as what products you have, how often they move and whether there are special storage requirements will shape your warehouse layout and operational processes. At the same time, the physical space of your warehouse, racking systems, handling equipment and security measures should also be examined in detail.
This initial analysis will clearly identify existing issues and areas for improvement. For example, issues such as congested aisles, poor lighting, or manual data entry can all negatively impact warehouse management efficiency. This comprehensive assessment will form the basis for your next steps and help you make your warehouse operations more efficient.
Errors Encountered in Warehouse Management
Establishing an effective warehouse management system is vital for businesses; however, some common mistakes made during this process can seriously reduce operational efficiency. Being aware of these mistakes and avoiding them will both reduce costs and increase customer satisfaction.
- Inadequate Inventory Tracking: Failure to track stock levels accurately can lead to situations such as excess stock or stock outs, which both increases costs and disrupts order fulfillment processes.
- Irregular Warehouse Layout: Storing products in an illogical or disorganized manner increases product retrieval times, increases the risk of incorrect shipments, and causes traffic problems within the warehouse.
- Inadequate Use of Technology: Over-reliance on manual processes increases data entry errors, increases labor costs and reduces warehouse management efficiency.
- Lack of Training: If warehouse personnel do not have adequate training, this can lead to incorrect operations, decreased productivity and safety risks.
- Lack of Feedback Mechanisms: Lack of regular feedback and analysis to identify disruptions and areas of improvement in processes causes problems to become chronic.
To avoid these common mistakes, it is essential to leverage technology, ensure ongoing training of staff, and regularly review processes. With a systematic approach, businesses can optimize their warehouse operations to gain competitive advantage and achieve sustainable growth.
Warehouse Management System Modules
Modern systems used for effective warehouse management usually consist of various modules that work in integration with each other. These modules cover different operational areas of the warehouse, ensuring that processes are carried out more regularly, without errors and efficiently. Each module serves a specific purpose while also contributing to the overall warehouse operation.
- Inventory Management Module: Provides real-time tracking of all products in the warehouse. Contains critical information such as stock levels, product locations, batch numbers and expiration dates. This module increases stock accuracy and minimizes unnecessary stock holding costs.
- Input-Output (Delivery Note) Module: Manages the acceptance processes, quality control steps and entry into the system of incoming goods. Similarly, it monitors the shipment preparations, loading processes and delivery note arrangements of products leaving the warehouse.
- Storage and Placement Module: Plans the most efficient positioning of products in the warehouse. It provides easily accessible areas for fast-moving products and offers optimum storage solutions for less demanded products.
- Order Picking Module: Ensures that products in customer orders are picked from the warehouse accurately and quickly. It can support different picking strategies (wave picking, batch picking, etc.) and increases efficiency with route optimization.
- Shipment and Loading Module: Manages the checking of collected and packaged products before shipment, loading them onto the correct vehicle and preparation of necessary documents. Ensures that shipments arrive on time and completely.
- Reporting and Analysis Module: Provides detailed reports and analysis on warehouse performance. It supports decision-making processes and ensures continuous improvement by tracking metrics such as stock turnover, order fulfillment time, accuracy rates.
The integrated operation of these modules simplifies complex warehouse management processes and provides businesses with end-to-end control, thus reducing operational disruptions, lowering costs and significantly increasing overall efficiency.
Warehouse Management with ERP Software
In today’s business world, manually executing warehouse management processes both leads to loss of time and increases the risk of errors. At this point, Enterprise Resource Planning (ERP) software offers great advantages to businesses by digitizing and centralizing warehouse operations. ERP systems allow integrated management of all warehouse activities from inventory to order fulfillment, from shipping to return processes on a single platform.
An ERP software allows warehouse personnel to access instant inventory information, process orders faster, and optimize shipments. For example, when a product enters the warehouse, its barcode is scanned through the ERP system and instantly added to the inventory, and this information is shared with other departments such as sales, finance, or production. This integration eliminates data inconsistencies and prevents interruptions in business processes. It also helps to make demand forecasts based on historical data, helping to keep inventory levels at optimum levels and avoid unnecessary storage costs.
Problems such as incorrect counts, incorrect product placements or delayed shipments, which are frequently encountered in manual processes, are minimized with an ERP system. The system reduces human error and standardizes processes by automating all steps. Thus, it enables businesses to work more efficiently, reduce costs and increase customer satisfaction, almost completely eliminating errors in warehouse management processes.
For more detailed information, you can check out our article titled Warehouse Management - A Guide for B2B E-Commerce Companies .